WE RIDE THE WORLD’S LIGHTEST CRF250:
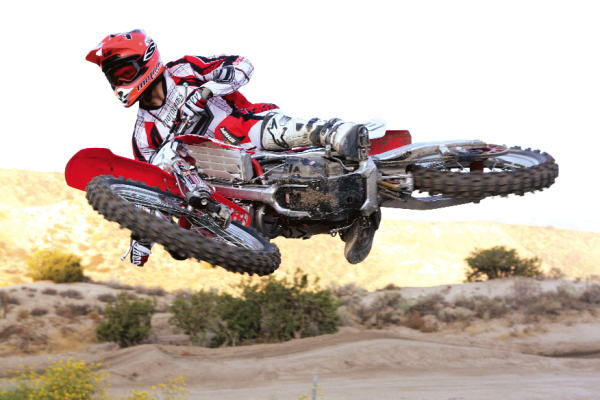
The Honda CRF250 is a very good motocross bike. Yes, it has flaws, but apart from the harsh Showa forks (left over from last year), superfluous muffler (a bad idea that won’t go away) and irritating bog (thanks to the 40mm carb), it has a solid powerband that is derived from Honda’s unique valve train and steady development process. But the question for every CRF250 owner is, what would you really want-?if your wants were posted in the R&D lab at HRC?
Don’t be mundane in your choices. Of course you want more power, better jetting and improved fork action. But be bolder with your demands. How about asking the Honda R&D department to build a 200-pound CRF250? Why not? Those are the ballpark weights of the 2009 YZ125 and KTM 125SX-?bikes that the 250cc four-strokes displaced. To get down to 125 two-stroke weights, the CRF250 would have to lose 17 pounds. That is a lot of weight to shave off of a bike that Honda feels is as light as it can be (for the price).
Price is always a factor when the subject of weight comes up. Americans spend $40 billion a year on diets. Lightweight road bicycles can cost as much as a CRF450. And it costs a Formula 1 team $6 million to build a car with a power-to-weight ratio of one horsepower per 1.77 pounds.
So when the MXA wrecking crew set out to build a 200-pound Honda CRF250, we realized that money would be the lube required to nudge the scale downward. Since a stock CRF250 has a power to weight ratio of one horsepower per 6.2 pounds, losing 17 pounds would improve that to one horsepower per 5.6 pounds. Obviously, if we could lower the weight even more, or increase the horsepower to National levels, we could get power-to-weight down to 1:5. That was our plan.
Losing weight on a motocross bike is easy; you simply replace every removable part with a lighter one (if such a thing exists). Here is where we whittled away at our CRF250.
(1) Fasteners. MXA went to CDG Technology (www.cdgtech.com), (530) 243-4451, for complete titanium and aluminum bolt and fastener kits. The chassis kit cost $1480, engine kit $1350, axles and pivots $1600, swingarm kit $900 and front end kit $900. These are all aerospace grade fasteners made in the U.S.A. and Western Europe. The weight savings was three pounds (most of the savings came from the axles).
(2) Titanium springs. Diverse Manufacturing Company (www.diverse-mfg.com), (661) 618-2644, provided a titanium shock spring and prototype Ti fork springs for MXA‘s project bike. The $500 shock spring saved 1.5 pounds, and the fork springs saved another pound (but isn’t available to the public yet).
(3) Titanium exhaust pipe. We used a single-sided FMF Factory 4.1 system with Mega-bomb header built by George Luttig (www.fmfracing.com), (310) 631-4363. It not only increased power by two horsepower, but it knocked over two pounds off of the “twice pipes” on the CRF250.
(4) Footpegs. Although footpeg weight is very low on the chassis, saving weight always benefits the power-to-weight ratio (even if it can’t be felt in the handling of the bike). MDK (www.mdkspeed.com), (408) 295-7437, makes very exotic $189 titanium footpegs that save 0.5 pounds over Honda’s skinny and heavy stock pegs.
(5) Gas tank. Way across the pond, in Italy, MXA tracked down a company that makes carbon fiber gas tanks for CRF250s. The CRM Composite carbon fiber gas tank was super exotic and super expensive. Unfortunately, it only saved 0.5 pounds over the stocker. For more info, go to www.crmcompositi.com. Prices vary with the Euro.
(6) Airbox. Where the carbon fiber gas tank was a letdown in the weight department, we struck gold with Twin Air. For a mere $1895, Twin Air (www.twinairusa.com), (800) 749-2890, offers a one-piece carbon fiber subframe and airbox for the CRF250. It was expensive, but shaved 2.5 pounds off of the weight of the stock airbox. Of course we used a Twin Air Bio Pre-Oiled Backfire Filter in it.
(7) Graphics. It may come as a surprise, but graphics kits are very heavy. MXA‘s project bike depended on Flu Designs (www.fludesigns.com), (661) 256-2313, to build us a special set of graphics using the thinnest 3M vinyl possible. Amazingly, we saved almost a pound over regular (and more durable) graphics.
(8) Triple clamps. Applied Racing was nice enough to build a special one-off, AZ31B magnesium top triple clamp (with Tiodize brand anodic coating) and a custom aluminum bottom clamp for MXA‘s project bike. In addition, Applied Racing (www.AppliedRace.com), (800) 853-0555, also spent some long hours custom machining various plastic parts, brackets, engine plugs, master cylinder covers, a brake hose clamp and attachments to help save weight.
(9) Wheels. When it came to saving weight on the Honda wheels, we discovered that Honda has wheels so light that most aftermarket wheelsets are heavier. TCR (www.tcrwheellacing.com), (209) 368-9800, came to our rescue with a set of wheels that were one pound lighter than the stockers.
(10) Carbon fiber. In addition to the CRM carbon fiber gas tank and Twin Air carbon fiber subframe/airbox, we installed a Lightspeed carbon fiber clutch cover, case guards, skid plate and rotor covers in place of the stock parts. You can contact Lightspeed at (www.lightspeedperf.com), (714) 990-5767.
(11) Miscellaneous. Weight is where you find it. To build a 200-pound CRF250, you have to be watchful. The stock fenders were replaced by Cycra plastic (and plastic was cut off in places where it overlapped other plastic). Works Connection supplied a full retinue of engine plugs, levers and perches (which Applied machined down to make even lighter). The stock Renthal 7/8-inch bars were replaced with lighter Renthal FatBars (made possible by the all-new Applied magnesium top clamp and bar mounts). Ride Engineering supplied the front brake hose billet clamp (and Applied machined it down), while Fasst offered its ultra-light aluminum rear brake clevis (of course, Applied machined it down even further).
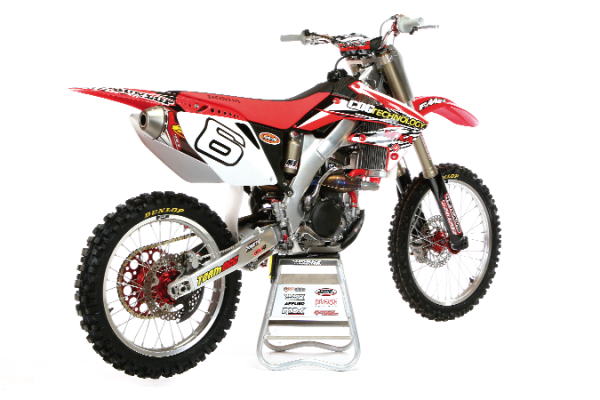
WHAT DID WE DO TO GET MORE POWER?
Part one of the power-to-weight ratio was expensive and time-consuming. Now that we had lowered the weight, we needed to increase the power.
(1) Engine. MDK Speed (www.mdkspeed.com), (408) 295-7437, took our CRF250 engine and gave the head its Stage 3 hop up ($2199). Our engine was totally rebuilt, and the work included porting, copper valve seats, titanium MDK intake and exhaust valves, stiffer valve springs (and retainers, platforms and Ti cotters), MDK piston (with gaskets), MDK camshaft, bored out 37mm carb (from the 2005 CRF250), Vortex ignition and MDK connecting rod (with DLC-coated pin).
(2) Suspension. MB1 (www.mb1suspension.com), (951) 371-5045, went whole hog on the CRF250 suspension. On the forks, the legs were DLC coated, and titanium fork and pressure springs were installed. The forks were revalved (something they need very much in stock trim). On the shock, MB1 revalved the damping, installed the titanium shock spring, replaced the stock steel shock collars with MB1 aluminum collars, mounted an oversize bladder cap, and DLC coated the shock shaft.
(3) Tires. We opted not to worry about weight when it came to tires–instead choosing to mount a Dunlop 756 rear tire and a Dunlop 756 Race Replica front tire (www.dunlopmotorcycle.com), (800) 845-8378. Our only nod to weight savings was to remove the stock rim strips and replace them with lighter tape.
(4) Transmission. In the tranny, CV4’s Rob Celendano did an ISF chemical process on the transmission that removed any imperfections in the surface of the parts (like machining marks, stress cracks, and other imperfections). The treated parts do not lose their actual tolerance, but drag and temperatures are decreased substantially. Horsepower is increased thanks to less mechanical loss and shifting is improved. Contact CV4 at www.cvproducts.com.
(5) Workmanship. Chad Watts of Watts Perfection (www.wattsperfections.com), (704) 538-9990, did all of the frame prep, including installing the inserts for the frame guards, and Thompson Race Works, (530) 347-4961, did the assembly work on the bike to get it back together after we got all the parts back from the suppliers.
VERDICT: WHAT DO WE THINK?
It is easy to think of a project like this in terms of statistics. We went from 217 pounds to 200 pounds and from 35 horsepower to 40 horsepower. The power-to-weight ratio dropped from one horsepower to every 6.2 pounds to one horsepower to every five pounds. But in truth, the proof is in the pudding.
We didn’t know what to expect from the bike’s diet, but it quickly became obvious that the weight savings would be most noticeable in straight-line acceleration and on the pitch/roll/yaw axis. It sounds so simple to say, “This bike felt light,” but it’s more than that. The lightness made everything easier. Sand whoops that sapped leg strength seemed smaller and easier to navigate. Deep ruts that tugged on the handlebars of the stocker seemed to melt when attacked with a lighter and more agile bike. Best of all, you could put MXA‘s 200-pound CR250 wherever you wanted it…and if you didn’t like where it went, you could muscle it back onto the correct line.
Losing weight is a weird concept, because the more money you spend, the more weight you lose…and the less you have to show for the money. We spent $10,000 to alter the power to weight ratio. How much are you willing to spend?
Comments are closed.